Don’t faint, there is nothing complicated here. We’ll explain everything now. But first, let’s clear the terminology. The fact is that many people mistakenly call an automatic transmission two units connected together: the gearbox itself and the torque converter.
The torque converter consists of two vaned machines – a propeller pump and a centripetal turbine. There is a guide apparatus, a reactor, between them. The impeller is rigidly connected to the crankshaft of the engine, the turbine – to the gearbox shaft. The reactor, depending on the operating mode, can rotate freely, or can be blocked with the help of an overrunning clutch.
The transmission of torque from the engine to the gearbox is carried out by flows of power fluid (oil) which is thrown by impeller blades on turbine blades. Minimal gaps are provided between the impeller and the turbine, and their blades are given a special geometry that forms a continuous circle of the power fluid circulation. So, it turns out that there is no rigid connection between the engine and the transmission. This ensures that the engine works and the car stops with the gear engaged, and also contributes to the smooth transmission of the traction force.
The hydraulic clutch can simply transmit the torque without transforming its value. To change the torque, a reactor is introduced into the design of the torque converter. This is the same wheel with blades, but it, having the connection with a housing (casing) of the gearbox, doesn’t rotate (note, up to a certain point). The reactor blades are located on the path along which the oil returned from the turbine to the pump, and they have a special profile. When the reactor is motionless (a torque converter mode), it increases the flow rate of the power fluid circulating between the wheels. The higher the speed of the fluid movement, the higher its kinetic energy, and the greater the impact it has on the turbine wheel. Thanks to this effect, the torque developed on the turbine wheel shaft can be significantly raised.
Imagine a standard situation – the gear is already engaged, and we are standing still and pressing the brake pedal! What happens in this case? The turbine wheel is stationary, and the torque on it is one and a half to two times higher (depending on the design) than what the engine develops at these revolutions. By the way, the higher the engine speed, the higher the torque on the output shaft of the torque converter. You just release the brake pedal, and the car starts. Acceleration will continue until the torque on the wheels is equal to the torque of the road resistance.
When the turbine wheel approaches the rotation speed of the pump wheel, the reactor wheel is released and begins to rotate together with two “partners”. In this case, they say that the torque converter has switched to the hydraulic clutch mode. This reduces losses and increases the efficiency of the torque converter.
And since there is no need to convert the torque and speed in some cases, the torque converter can be completely blocked at certain moments with the help of a friction clutch. This mode helps to bring the transmission efficiency to almost one, slippage between bladed wheels is, by definition, impossible in this case.
But imagine such a situation. You are driving in a straight line and suddenly start to climb. The speed of the car will begin to fall, and the load on the driving wheels will increase. The torque converter will immediately respond to this change. As soon as the turbine rotation speed decreases, the reactor wheel will automatically slow down, as a result, the speed of circulation of the power fluid will increase, which will automatically lead to an increase in the torque that will be transmitted to the shaft from the turbine wheel (think to the wheels). In some cases, the increased torque is enough to climb a gradient without switching to a lower gear.
Since the torque converter can’t convert the speed of rotation and the transmitted torque within a wide range, a multi-speed gearbox is attached to it, which, in addition, is able to provide reverse rotation (in other words, back run). Those boxes that work in tandem with torque converters usually include a number of planetary gears and have a lot in common with manual gearboxes that are familiar to us.
In a manual gearbox, the gears are in constant engagement, while the driven ones rotate freely on the secondary shaft. By shifting into any gear, we mechanically block the corresponding gear on the driven shaft. The operation of the automatic transmission is based on the same principle. But planetary reduction gears have some interesting features. They include several elements: a pinion carrier, pinion gears, sun and annular gears.
By rotating some elements and fixing others, such reduction gears can change gear ratios, that is, the speed of rotation and the force transmitted through the planetary gear. Planetary gears are driven from the output shaft of the torque converter, and their corresponding elements are fixed with friction bands and friction packs (in a mechanical gearbox, this role is played by synchronizers and lockup clutches).
The transmission is engaged as follows. The clutch is pressed by a hydraulic tappet, which in turn is actuated by the pressure of the power fluid, the one that is used in the torque converter. This pressure is created by a special pump, and it is distributed between the corresponding gear clutches under the firm control of electronics by the use of a special system of electromagnetic solenoid valves in accordance with the algorithm of the box.
A significant difference between automatic transmissions and conventional manual transmissions is that the gears in the first ones are changed almost without an interruption in torque delivery. One is engaged, the other is disengaged almost at the same moment. Strong jerks during switching are almost eliminated, since they are dampened by the torque converter already mentioned above. Although, it should be noted, modern gearboxes with a sports setting can’t boast of smooth operation. Jerks during their operation are caused by a faster change of gears: this arrangement allows to save a certain amount of time during acceleration, but leads to accelerated wear of the clutches. This also affects the transmission and chassis as a whole in a bad way.
The control systems were entirely hydraulic in automatic transmissions of the first generation. Later, hydraulics were retained only as an executive part of the control system. Thanks to it, it is possible to implement various algorithms for the operation of the box – hard acceleration, sport, economy, winter modes…
In sport mode, for example, the engine thrust is used one hundred percent. The engagement of each subsequent gear occurs at crankshaft frequencies at which the maximum torque develops. With further acceleration, the rotational speed of the crankshaft is brought to the maximum values at which the engine develops maximum power. And so on. In this case, the car develops significantly greater accelerations compared to those carried out during the operation of economy and normal programmes.
On most modern cars with automatic transmission, certain control algorithms are activated depending on the driving style. Electronics adapt the operation of the engine-transmission tandem by itself. The computer, analyzing the information from numerous sensors, makes a decision to change gears at certain moments, depending on the required nature of the shifts. If the driving manner is measured and smooth, the controller makes appropriate corrections in which the engine doesn’t operate in power modes, which has a positive effect on fuel consumption. As soon as the driver “gets nervous” and begins to press the gas pedal more often and sharply, artificial intelligence immediately understands that speeding and acceleration must be done faster, and the power unit will immediately start working according to the sport program. If the driver pedals smoothly, the “smart” electronics will switch the gearbox and the engine to normal operation.
An increasing number of cars are equipped with gearboxes in which, along with automatic, a semi-automatic control mode is also provided. Here, the driver gives the commands to change gears, and the control system provides the switches. But this doesn’t mean that electronics will allow you to go wild. The speed of switching from one gear to another is often increased in this mode, but many manufacturers keep the switching time the same as in automatic mode, taking care of the power unit’s life. Car builders call these systems in different ways – Autostick, Steptronic, Tiptronic.
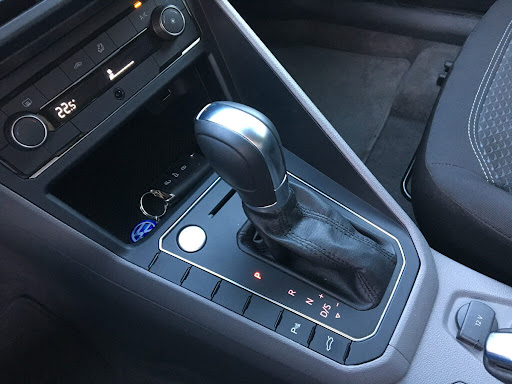
By the way, recently some automatic transmissions can be tuned. And this became possible due to the reprogramming of the engine control units and the gearbox. For the sake of acceleration speed, the moments of gears’ changing in the automatic transmission control program are changed and the switching time is significantly reduced.
Electronics are getting smarter from year to year. Computers have been taught to analyze the degree of friction wear and generate the appropriate pressure required to engage each clutch. By registering the pressure, it is possible to predict the degree of wear of the friction disks, and hence, the gearbox as a whole. The control unit constantly monitors the serviceability of the system, recording the fault codes of those elements in which failures occurred during operation.
The control unit starts working according to the bypass program in some force majeure cases. Usually, all shifts are prohibited in the gearbox in emergency mode, and any one gear is engaged, as a rule, the second or third. In this case, it is not recommended to operate the car (and it will not work), but the program will help you get to the repair shop under its own power.
All types of gearboxes are able to bring joy to car owners with their service with a run of more than 200 thousand kilometers. But there is one thing – trouble-free operation is possible with proper maintenance and regular qualified inspection.
Automatic transmission modes
P – parking. In this mode, all gears are disengaged, the output shaft of the gearbox and the transmission line connected to the driving wheels are locked by the locking mechanism of the box. With the operating engine, the crankshaft speed limiter is triggered much earlier than during acceleration. This “foolproof” doesn’t allow you to strain the engine and shovel the transmission fluid to no avail.
R – reverse.
N – neutral. In this mode, the engine and drive wheels aren’t connected. The car can coast, it can also be towed without lifting the driving axle.
The D or Drive mode allows you to move. In this mode, the gears are changed automatically.
The S, Sport, PWR, Power of Shift mode is the most dynamic and the most wasteful. During acceleration, the engine is driven into the maximum power mode. The speed of gear shifting (depending on the design and program) can be increased. The engine in this case is always toned, as a rule, working at speeds that aren’t lower than those at which the maximum torque develops. Forget about economy.
Kick-down is a mode in which the downshift is carried out for intensive acceleration, for example, when overtaking. A sharp pick-up occurs due to the fact that the engine is put into maximum efficiency, and due to a greater transmission ratio of the reduction gear. In order for the transmission to switch to this mode, you need to stomp on the gas pedal properly. In transmissions of an older generation, it was necessary to put the gas pedal, as they say, “to the metal”, until there was a characteristic click, to trigger Kick-down.
When operating in the Overdrive or O/D mode, the overdrive gear will be engaged more often, putting the engine at a reduced speed. Overdrive provides efficient driving, but its activation can lead to significant loss in dynamics.
Norm implements the most balanced driving mode. Upshifts, as a rule, occur when the average engine speed is reached and at speeds slightly above average.
If you put the selector on “1” (L, Low), “2” or “3”, your gearbox won’t shift up above the selected gear. The modes are in demand in severe road conditions, for example, when driving on mountain roads, towing a trailer or other car. In this case, the engine can operate in the range of medium and high loads without an upshift.
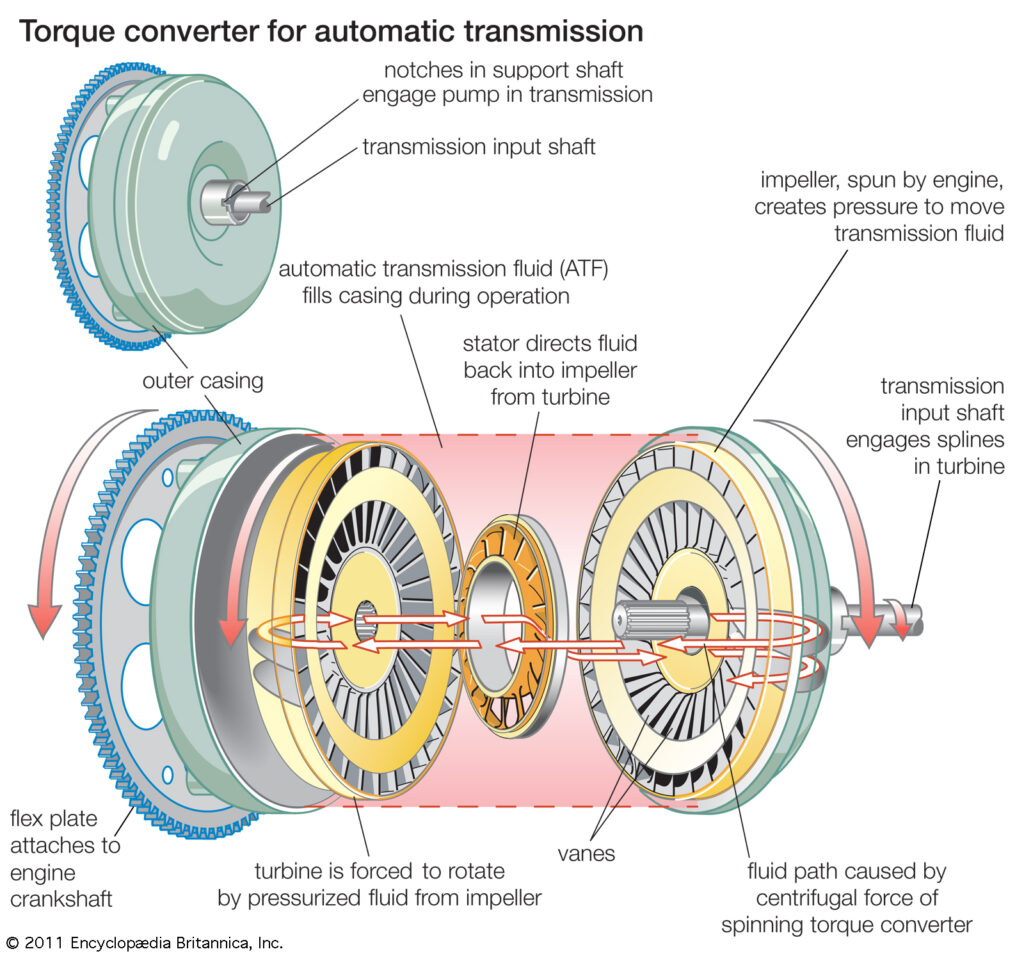
W, Winter, Snow – in order to prevent slipping of the driving wheels, the car starts with the second gear in this mode. In order not to cause unnecessary slippage, the gears can be changed more gently and at lower speeds. At the same time, acceleration may not be too dynamic.
“+” and “-” signs determine not the pole position, but the possibility of manual gear shifting. Different manufacturers allow you to “mix” the gears in different ways: with an automatic transmission selector, buttons on the steering wheel or steering-wheel-mounted paddle shifters. In this mode, electronics will not allow you to switch to those transmissions that, in its opinion, are inappropriate at the moment. When operating with “addition” and “subtraction” signs, the speed of the change of gears won’t be higher than that set by the program in the Sport mode. The advantage of the manual mode is the ability to act ahead of the curve.
This is a translation. You can read the original here: https://www.drive.ru/technic/4efb330d00f11713001e3660.html
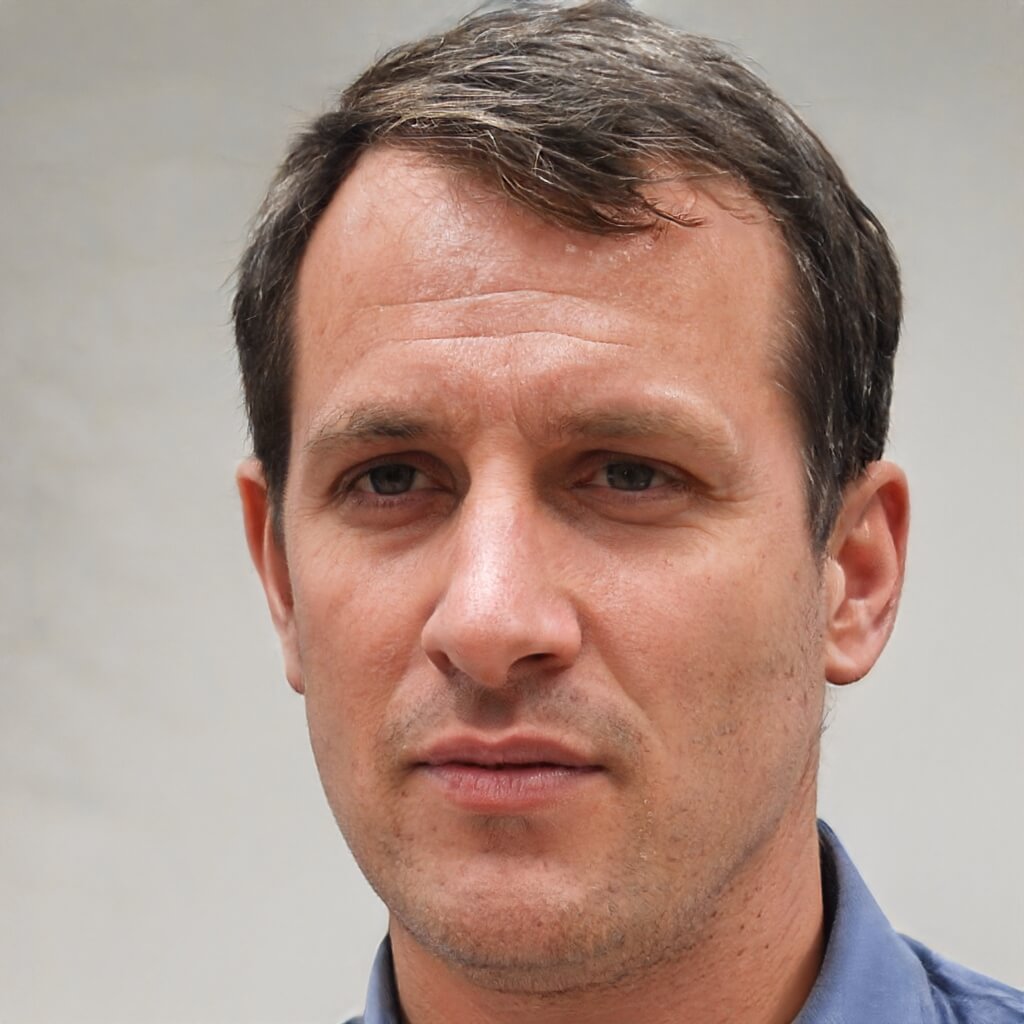
Published December 30, 2021 • 11m to read