Não há dúvida de que cada um de nós já notou a placa de identificação “turbo” em um carro de aparência comum pelo menos uma vez na vida. Como se fossem de propósito, os fabricantes fabricam essas placas de identificação de tamanho pequeno e em locais discretos, para que um transeunte não iniciado não perceba e passe. E uma pessoa consciente certamente parará e se interessará pelo carro. A seguir, uma história sobre os motivos desse comportamento.
Os projetistas automotivos (a partir do momento em que essa profissão surgiu) estão constantemente preocupados com o problema do aumento de potência do motor. As leis da física afirmam que a potência do motor depende diretamente da quantidade de combustível queimado em um ciclo de trabalho. Quanto mais combustível queimamos, maior a potência. E, digamos, queremos aumentar o “número de cavalos” sob o capô – como fazer isso? É aí que enfrentamos os problemas.
O fato é que o oxigênio é necessário para a queima de combustível. Portanto, não é um combustível, mas uma mistura ar-combustível que queima em cilindros. É necessário misturar combustível com ar não a olho nu, mas em uma determinada proporção. Por exemplo, uma mistura para motores a gasolina é composta por uma parte de combustível e 14 a 15 partes de ar – dependendo do modo de operação, da composição do combustível e de outros fatores.
Como podemos ver, é necessário muito ar. Se aumentarmos o suprimento de combustível (isso não é um problema), também teremos que aumentar significativamente o suprimento de ar. Os motores convencionais o atraem devido à diferença de pressão no cilindro e na atmosfera. A dependência acaba sendo direta – quanto maior o volume do cilindro, mais oxigênio entrará nele em cada ciclo. Foi o que os americanos fizeram, produzindo motores enormes com um consumo de combustível impressionante. Mas existe uma maneira de bombear mais ar para o mesmo volume?
Existe, e foi inventado pelo Sr. Gottlieb Wilhelm Daimler. Esse sobrenome é familiar para você? Obviamente, ele é usado no nome DaimlerChrysler. Então, esse alemão era muito bom em motores e, em 1885, ele inventou a maneira de bombear mais ar para eles. Ele teve a ideia de bombear ar para os cilindros usando um superalimentador, que era um ventilador (compressor) que recebia rotação diretamente do eixo do motor e bombeava ar comprimido para os cilindros.
O engenheiro e inventor suíço Alfred J. Büchi foi ainda mais longe. Ele era responsável pelo desenvolvimento de motores a diesel na empresa Sulzers Brothers e não gostava absolutamente do fato de os motores serem grandes e pesados e desenvolverem pouca potência. Ele também não queria tirar energia do motor para girar o compressor de acionamento. Portanto, em 1905, o Sr. Büchi patenteou o primeiro dispositivo de carregamento de ar do mundo, que usava a energia dos gases de escape como fonte de energia. Simplificando, ele inventou a turbocompressão.
A ideia do suíço inteligente é tão simples quanto tudo que é engenhoso. Os gases de escape giram uma roda de pás à medida que os ventos movem as velas do moinho. A única diferença é que a roda é muito pequena e tem muitas lâminas. Uma roda de pás é chamada de rotor de turbina e é montada em um eixo com a roda do compressor. Então, convencionalmente, o turbocompressor pode ser dividido em duas partes – um rotor e um compressor. O rotor recebe rotação dos gases de escape e o compressor conectado a ele bombeia ar adicional para os cilindros, funcionando como um “ventilador”. Toda essa construção intrincada é chamada de turbocompressor (das palavras latinas “turbo” – vórtice e “compressio” – compressão).
Em um motor turbo, o ar que entra nos cilindros geralmente precisa ser resfriado adicionalmente – então, sua pressão pode ser aumentada bombeando mais oxigênio para o cilindro. Afinal, é mais fácil comprimir o ar frio (já no cilindro do motor de combustão interna) do que o quente.
O ar que passa pela turbina é aquecido por compressão, bem como pelas partes turboalimentadoras aquecidas pelos gases de escape. O ar fornecido ao motor é resfriado com o uso de um intercooler. Este é um radiador instalado no caminho do ar do compressor até os cilindros do motor. Ao passar por ele, ele dá calor à atmosfera. E o ar frio é mais denso, o que significa que ainda mais ar pode ser bombeado para o cilindro.
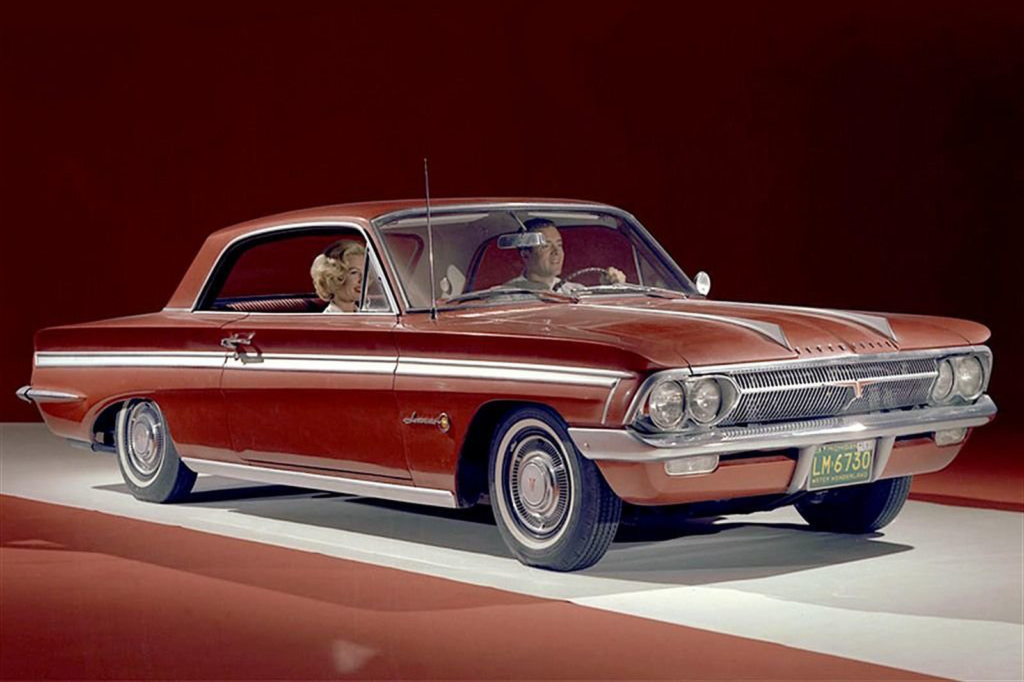
Quanto mais gases de escape entrarem na turbina, mais rápido ela gira e quanto mais ar adicional entrar nos cilindros, maior será a potência. A eficiência dessa solução em comparação, por exemplo, com um superalimentador de acionamento é que pouquíssima energia do motor, apenas 1,5%, é gasta na “automanutenção” do carregamento. O fato é que o rotor da turbina recebe energia dos gases de escape não por meio de sua desaceleração, mas por meio de seu resfriamento – depois da turbina, os gases de escape ainda são rápidos, mas mais frios. Além disso, a energia livre gasta na compressão do ar aumenta a eficiência do motor. E a capacidade de obter mais potência com um volume de trabalho menor significa menos perdas por atrito, menos peso do motor (e do carro como um todo). Tudo isso torna os carros turboalimentados mais eficientes em termos de combustível em comparação com seus equivalentes atmosféricos da mesma potência. Parece que isso é felicidade. Mas não, não é tão simples. Os problemas estão apenas começando.
Em primeiro lugar, a velocidade de rotação da turbina pode chegar a 200 mil rotações por minuto e, em segundo lugar, a temperatura da lâmpada incandescente atinge, imagine, 1000°C! O que tudo isso significa? É muito caro e difícil fabricar um turbocompressor capaz de suportar cargas tão pesadas por muito tempo.
Por esses motivos, a turbocompressão se difundiu apenas durante a Segunda Guerra Mundial e somente na aviação. Nos anos 50, a empresa americana Caterpillar conseguiu adaptá-la aos seus tratores, e os mestres da Cummins projetaram os primeiros turbodiesel para seus caminhões. Os motores turbo apareceram em carros de passageiros em série ainda mais tarde. Aconteceu em 1962, quando o Oldsmobile Jetfire e o Chevrolet Corvair Monza foram lançados quase simultaneamente.
Mas a complexidade e o alto custo do design não são os únicos inconvenientes. O fato é que a eficiência da turbina depende fortemente da velocidade do motor. Em baixas velocidades, o volume dos gases de escape não é muito, o rotor gira mal e o compressor quase não sopra ar adicional nos cilindros. Portanto, acontece que o motor não anda a menos de três mil rpm e só então, depois de quatro ou cinco mil, ele “dispara”. Essa mosca na pomada é chamada de atraso do turbocompressor. Além disso, quanto maior a turbina, mais ela ganhará velocidade. Portanto, motores com relação potência/peso muito alta e turbinas de alta pressão, via de regra, sofrem particularmente com o atraso do turbocompressor. Mas as turbinas que criam baixa pressão quase não têm turbo-lags, mas não aumentam muito a potência.
Um esquema de turboalimentação sequencial ajuda a quase eliminar o turbo-lag. Em baixas rotações do motor, um pequeno turbocompressor de baixa inércia funciona, aumentando o empuxo na “parte inferior”, e o segundo, maior, liga em altas velocidades com o aumento da pressão de escape. No século passado, um turbocompressor sequencial foi usado no Porsche 959 e hoje, por exemplo, os turbodiesel BMW e Land Rover são organizados de acordo com esse esquema. Nos motores a gasolina da Volkswagen, o papel de uma pequena “potência” é desempenhado por um superalimentador de acionamento.
Em motores retos, um único turbocompressor de rolagem dupla (um par de volutas) com um aparelho de trabalho duplo é frequentemente usado. Cada uma das volutas é preenchida com gases de escape de diferentes grupos de cilindros. Mas, ao mesmo tempo, ambos fornecem gases para uma turbina, girando-a efetivamente em velocidades baixas e altas.
Mas ainda é mais comum encontrar um par de turbocompressores idênticos servindo grupos separados de cilindros em paralelo. Um esquema típico para motores turbo em forma de V, em que cada unidade tem seu próprio superalimentador. Embora o motor V8 da M GmbH, que estreou no BMW X5 M e X6 M, esteja equipado com um coletor de escape transversal, que permite que o compressor twin-scroll receba gases de escape dos cilindros de diferentes blocos operando na fase oposta.
Também é possível fazer com que o turbocompressor funcione com mais eficiência em toda a faixa de velocidade, alterando a geometria da peça de trabalho. Dependendo da rotação dentro da voluta, as lâminas especiais giram e o formato do bico varia. O resultado é uma “superturbina” que funciona bem em toda a faixa de velocidade. Essas ideias estavam no ar há décadas, mas foram implementadas há relativamente pouco tempo. Além disso, inicialmente turbinas com geometria variável apareceram em motores a diesel, felizmente, a temperatura dos gases lá é muito menor. E o Porsche 911 Turbo foi o primeiro carro a gasolina a experimentar essa turbina.
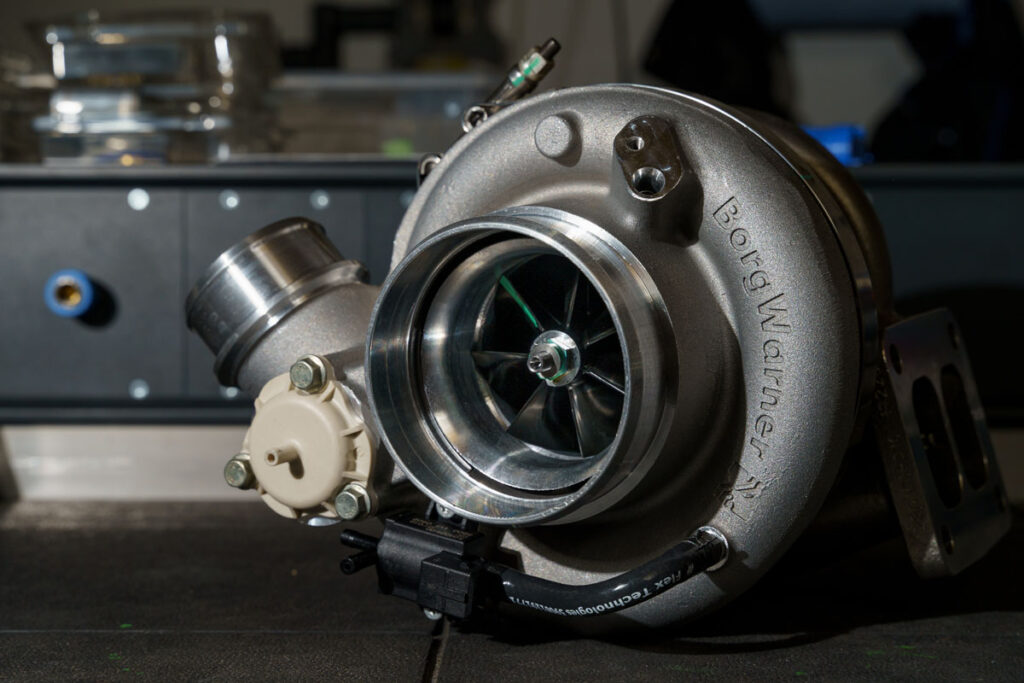
O design dos motores turbo entrou em forma há muito tempo e, recentemente, sua popularidade aumentou dramaticamente. Além disso, os turbocompressores se mostraram promissores não apenas em termos de força do motor, mas também em termos de aumento da eficiência e pureza do escapamento. Esse é especialmente o caso dos motores a diesel. Quase todo diesel tem o prefixo turbo hoje. Ao mesmo tempo, a instalação de uma turbina em motores a gasolina permite transformar um carro de aparência comum em um verdadeiro “isqueiro”. Aquele com uma placa “turbo” pequena, quase imperceptível.
Esta é uma tradução. Você pode ler o original aqui: https://www.drive.ru/technic/4efb330200f11713001e3303.html
Publicado January 27, 2022 • 8m to read