The performance quality of the engine, its efficiency, power, torque, operational economy, depend on many factors, including valve timing, that is, the timeliness of the intake and exhaust valves’ opening and closing.
In a conventional four-stroke internal combustion engine, the valves are actuated by camshaft cams. The profile of these cams determines the torque and the duration of the opening (i.e. the width of the phases), as well as the stroke of the valves.
Phases can’t be changed in most modern engines. And the operation of such engines is not very efficient. The fact is that the nature of the behavior of gases (fuel mixture and exhaust) in the cylinder, as well as in the intake and exhaust ports varies depending on the operating modes of the engine. The flow velocity is constantly changing, various kinds of vibrations of the elastic gas medium, which lead to useful resonant, or, conversely, parasitic congestion, arise. Because of this, the speed and efficiency of the cylinders’ filling are not the same under different engine operating modes.
For example, for idling operation, narrow valve timing phases with late opening and early closing of valves without overlapping phases (the time when both the intake and exhaust valves are open) are appropriate. Why? Because in this way it is possible to exclude the discharge of exhaust gases into the intake manifold and the release of part of the combustible mixture into the exhaust pipe.
The situation changes a lot when working at maximum power. With an increase in speed, the time of the valves’ opening naturally decreases, but to provide high torque and power through the cylinders, it is necessary to run a much larger volume of gases than at idle. How to solve such a difficult task? Open the valves a little earlier and increase the duration of their opening, in other words, make the phases as wide as possible. At the same time, the overlap phase is usually made the wider the higher the rpm for better drainage of the cylinders.
So designers have to link a number of mutually exclusive requirements and make difficult compromises when developing and fine-tuning engines. Judge for yourself. With the same fixed phases, the engine should have good traction at low and medium speeds, an acceptable power at high speeds. And plus, percolate at idle, be as efficient and environmentally friendly as possible. That’s the problem!
But these tasks have been as easy as shelling peas for designers for a long time – they are able to change the characteristics of the engine beyond recognition by shifting and changing the width of the valve timing phases. Need to increase the torque? Okay. Increase the power? Of course. Reduce consumption? Not an issue. However, it turns out sometimes that you have to sacrifice some parameters in order to improve others.
But what if the gas distribution mechanism will be taught to adapt to different engine operating modes? Easily. Fortunately, there are a lot of ways to do this. One of them is the use of a phase shifter – a special clutch that is capable of turning the camshaft at a certain angle relative to its initial position under the influence of control electronics and hydraulics. Such a system is most often installed at the intake. With an increase in speed, the clutch turns the shaft in the course of rotation, which leads to an earlier opening of the intake valves and, as a result, better filling of the cylinders at high speeds.
But irrepressible engineers didn’t stop there and developed a number of systems that can not only shift the phases, but also to widen or narrow them. This can be achieved in several ways, depending on the design. For example, in the Toyota VVTL-i system, an additional cam with a modified profile begins to come into operation instead of the usual cam after reaching certain revolutions (6000 rpm). The profile of this cam sets a different law of valve movement, wider phases and, by the way, provides a longer stroke. When the crankshaft is spun up to maximum rpm (about 8500 rpm), at a rotation speed of 6000-6500 rpm, the engine seems to get a second wind, which is able to give the car a hard and powerful pick-up during acceleration.
It is wonderful to change the torque and duration of the opening. And what if we try to change the height of the lift? After all, this approach allows you to get rid of the throttle and shift the process of controlling the engine operating modes to the valve train.
Why is the throttle valve harmful? It worsens the filling of the cylinders at low and medium speeds. After all, a high vacuum is created in the intake tract under the closed throttle when the engine is running. What does it lead to? To a high inertia of the rarefied gas medium (fuel-air mixture), a deterioration of the quality of the cylinder’s filling with a charge, a decrease in the engine output and in the gas pedal response speed.
Therefore, to open the intake valve only for the time necessary to achieve the desired filling of the cylinder with a combustion mixture would be an ideal option. The engineers’ answer is a mechanical intake valve lift control system. In such systems, the lifting height and, correspondingly, the duration of the intake phase are changed depending on the depressing of the gas pedal. According to various sources, savings from the use of a throttleless control system can range from 8% to 15%, an increase in power and torque – in the range of 5-15%. But this is not the last stand.
Despite the fact that the number and size of valves have approached the maximum possible, the efficiency of filling and cleaning of the cylinders can be made even higher. Due to what? Due to the valves’ opening speed. However, the mechanical drive loses its ground to the electromagnetic one.
What is another advantage of the electromagnetic drive? The fact is that the law (acceleration at any time) of valve lifting can be perfected, and the duration of valve opening can be changed within very wide limits. Electronics, according to the configured program, may not open unnecessary valves from time to time, and deactivate the cylinders at all. What for? In order to save money, for example, at idle, when driving in steady mode or when braking with the engine. In addition to the modes, the electromagnetic valve train is able to turn an ordinary four-stroke engine into a six-stroke one right during operation. We wonder if such systems will appear on the assembly line soon.
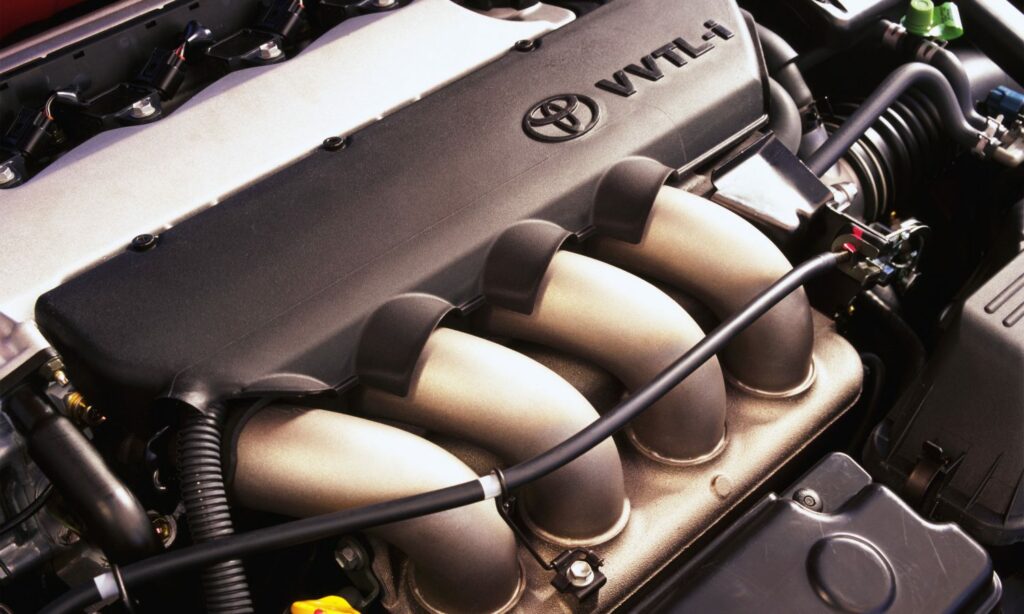
Perhaps, it’s no longer possible to further increase the efficiency of the engine due to timing. It will be possible to get even more power and torque from the same volume with less consumption only with the use of other means. For example, combined supercharging or constructions that change the compression ratio, other fuels. But this is a completely different story.
This is a translation. You can read the original here: https://www.drive.ru/technic/4efb330700f11713001e33f9.html
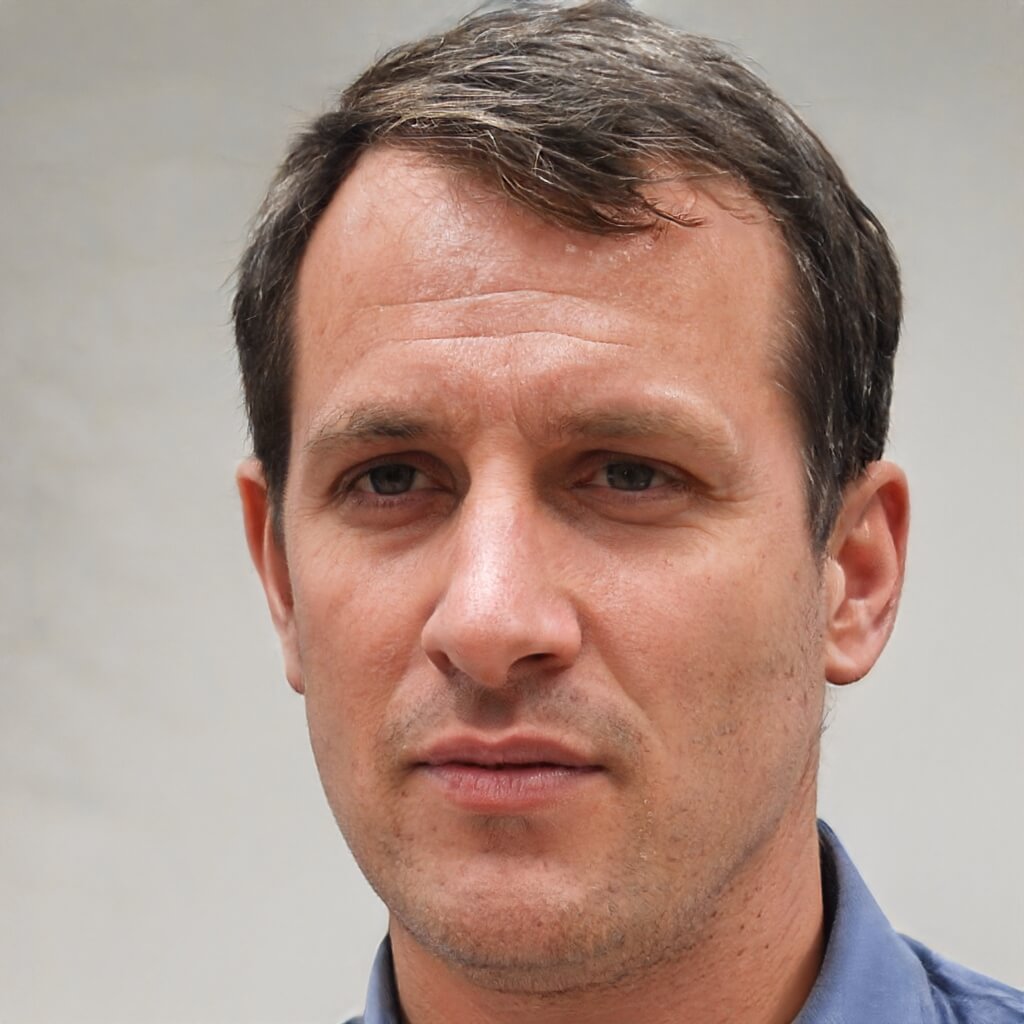
Published January 13, 2022 • 5m to read