Each of us determines the importance of certain consumer properties of a car. For example, someone is more interested in spaciousness, and someone – in steerability. But acoustic comfort is relevant for everyone. You don’t need to be an expert to know if a car is noisy. The first conclusions can be made literally at the beginning of your trip. At the same time, assessment of the running smoothness or brakes takes time. In the industry, there is a combined concept of NVH (Noise, Vibration, Harshness).
If everything is bad in the NVH sphere, a person physically feels it: nervous system and brain are overloaded, concentration is impaired, tone and reaction decrease. Therefore, it is easier to drive long distances in modern quieter cars. Please don’t think that “the sound insulation has become better over time”! In theory, sound insulation is the last and not necessarily the most effective way to provide acoustic comfort. Now let’s understand why.
It is difficult to talk about NVH without deep immersion in physics and mathematics. In order for us not to get stuck in lofty matters, we will simplify some things. But it is not wrong to say that the noise is generated by vibrations. The latter themselves are also harmful, especially for technical equipment.
So, any vibration has a source. Car noises and vibrations are generated primarily by engine and exhaust system, rolling wheels, and air flowing around the body. There are another few dozen sources, but it is the ones listed above that dominate. Usually, at urban speeds, the main “contribution” is made by the power unit, everything “sings” almost equally on the highway’s 90-100 km/h, and after 120-130 km/h, the first concern is the disturbances of aerodynamic and road origin. This is in theory.
Any noise, such as one from an engine, propagates in two ways. Mechanically – through the vibrations of the body panels and structural elements that have a physical connection with the source, and directly through the air, including “penetrating” through the same panels. Therefore, there are three main ways to deal with noise. In priority order, this is a reduction in the intensity of its origin, the attenuation of secondary radiation by structural elements, and only in the third place ― sound insulation, that is, “catching” the component that is transmitted by air.
For example, the abatement of engine noise begins with the organization of the combustion process, which should be smoothed out if possible. Large sound emitters ― the cylinder block, the head cover, the sump – are designed so as not to resonate in time with the working process in the cylinders. More and more often such elements are made of plastics, noise-absorbing materials are applied directly to them, and the entire engine is “encapsulated” if possible. Exhaust systems used to make a lot of noise, but catalysts and particulate filters, that smooth out pulsations of exhaust gases to support the exhaust silencers, unwittingly helped.
Further transmission of vibrations should be prevented by supports of the power unit. The points of their attachment are chosen so as not to provoke body vibrations. The history of the first serial VAZ-2108 is memorable, in which vibrations and noise at idle reached an uncomfortable level due to an incorrectly located front support. It was too late to move the support, it was made softer, which brought a number of other problems…
Today, hydraulic supports of the power unit, which combine an elastic and suppressing function (like a duet of a spring and a shock absorber in the suspension), are no longer exotic. Active supports that create movement in the opposite phase to vibration or change their rigidity depending on the conditions are the most effective.
Vibrations that still reach the body should be minimized. It is very important to avoid resonances. The maximally rigid body doesn’t necessarily turn out to be quiet. Monolithic construction can reduce resonances, but increase structural noise transmission.
Unlike journalists, automotive engineers often use the concept of resonant frequencies of the body, rather than its torsional rigidity. Moreover, the optimal frequency shouldn’t be as high or low as possible ― it should be exactly such as to avoid resonances. Because the body is only one of the members of the most complex vibration system, which includes elastic suspension elements, tires, seats, and all sources of vibration.
The load-bearing arrangement of the body is developed taking into account all of the above. Even those parts that don’t carry a serious load, have stiffener bars and stamped reinforcement plates to counteract vibrations as much as possible. High-strength and heat-treated steels, rolling of variable thickness, technologies for gluing body parts and other tricks are used even in the mass automotive industry. At the same time, the computer simulation will still detect residual vibrations. What should you do with them?
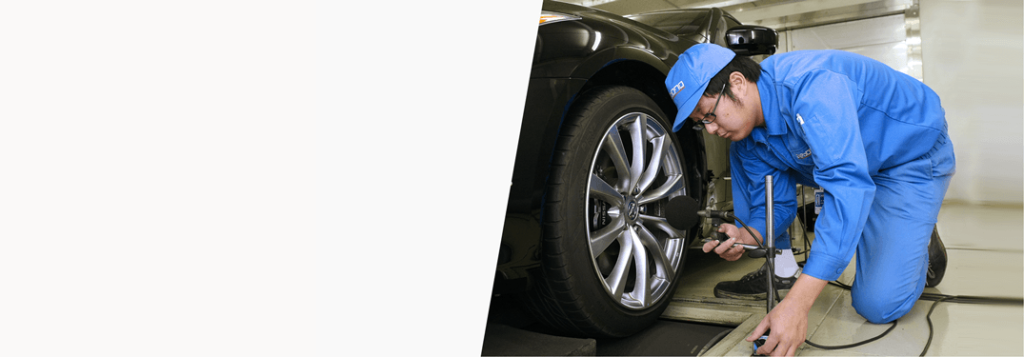
In a nutshell, you need to change the frequencies of natural vibrations at such points to avoid resonance. For example, by using vibration dampers – rigidly or softly fixed masses. Don’t be surprised to find a three-kilogram cast-iron bar somewhere in the bowels of the front bumper when repairing: it wasn’t forgotten here at the factory, but was screwed strictly according to the design calculation in order to level out the fluctuations of certain frequencies. Smaller loads are often placed on parts of the suspension or exhaust system.
Foam, which resembles construction one with its characteristics, is poured into the body cavity in certain places, and bitumen mats, for example, are glued to flat panels. But not all over, as in garage tuning, but selectively, with a choice of places based on computer modeling. Noise uses any loopholes, so the number of them in the body, and especially in the engine shield, is minimized. Any of them is carefully isolated. It is good that mechanical drives of the accelerator and automatic transmissions, which served as a powerful channel for transmitting vibrations, are a thing of the past. And only after all the design reserves are selected, it is time for sound insulation.
If everything is done correctly in the previous stages, you won’t need much of it. For example, four kilograms less noise insulation materials were used for the seventh-generation Golf than for its predecessor. Modern soft mats and carpets are technological masterpieces, precisely molded to the contours and relief of the engine shield or floor. In the car interior, you can’t do without a covering at all, because it also performs a thermal insulation function. But don’t be surprised, for example, by the bare metal around the spare wheel in the trunk — this means that, according to the manufacturer, the noise has been successfully suppressed by primary measures.
Such “protocols” are applied not only to the noise from the engine, but also to each source. Believe us, we can write about the fight against the rumble of rolling tires, aerodynamic disturbances or external sounds in separate articles. There are a lot of nuances, subtleties and tricks. Home made pasting with additional mats certainly has an effect, but this approach can’t be called rational. You will not only have to spend a lot of money on materials and work for a couple of decibels of advantage, but also carry dozens of extra kilograms with you, paying for them with increased fuel consumption.
The latest trend is active noise reduction systems which use speakers of the audio system to create useful sound in the opposite phase to harmful one. One with another should give silence. Alas, such systems don’t work accurately, they are limited in power and frequency range: it’s physics. Noise from the engine and the road reaches the ears of the driver and passengers in just 0.009 seconds, and the best anti-systems react in 0.002 seconds. It is clear that they will improve ― but the main thing is not to get the same situation as with ESP, when the development of safety electronics turned into a weakening of the basic design principles…
The higher the frequency of the sound, the more disturbing it is. For example, the fatigue effect starts at a volume of 80 decibels (dB) in the frequency range of 2000-4000 Hz, and already with 60 dB at 5000-6000 Hz. Structural noises, which are propagated by the body, mainly have a frequency below 500 Hz and are perceived by ear as more low-frequency, humming, bass. In a car, they mostly come from the road, but there is also a contribution from the exhaust system.
And the disturbances that are transmitted acoustically dominate at frequencies above 1000 Hz (they are considered high-frequency after 800 Hz). Here, the power unit and aerodynamics mainly make noises. A person perceives sound in the range of 20 Hz to 20,000 Hz, but we usually have to deal with 30-8500 Hz in a car.
In addition to the spectral composition (noise frequency), the nature of the spectrum is also important. There are broadband noises, that is, a mix of sounds, and tonal noises. For example, the howling of the power steering’s electric motor or the wheezing of the refrigerant in the bowels of the air conditioner. A car can produce hundreds of such specific “notes”, and good manufacturers “destroy” them completely at the stage of road testing.
By the way, the noise volume value in decibels doesn’t necessarily correspond to the subjective feelings of a person. At least because our hearing organ perceives sounds of different frequencies differently. Yes, noise meters also process signals from the microphone in a complex program, trying to copy the sensitivity of the ear. But it doesn’t always work. In practice, automakers necessarily focus not only on measurements, but also on the opinion of experts. Sometimes it is easier to transfer the sound to a more pleasant frequency than to suppress it. All this is solved during road tests.
There are no restrictions on the internal noise of passenger cars either in the EU or in the US ― only on the external one. It is clear that manufacturers are vitally interested in making the customer comfortable in the interior. But, for example, Russia has its own way. During certification, all new cars, including Rolls-Royce or Mercedes-Maybach S-class, are checked for compliance with Annex No. 3 to the technical regulations “On the Safety of Wheeled Vehicles”. That is, they actually hang microphones in the cabin and measure noise using several methods ― including when driving at a constant speed and during acceleration.
In general, the noise shouldn’t exceed 77 dB, but there are a lot of exceptions. 79 dB are already allowed for cars of wagon and semi-cab layout, such as minivans. If the car is certified as an SUV (this is done even with some crossovers), these values can be exceeded by two decibels. At one time, the collectable Porsche 911 R coupe didn’t get to Russia precisely because of non-compliance with specific requirements for the level of internal noise.
Although a separate footnote is provided for sports cars. If the curb weight is less than two tons, and the power-to-weight ratio is higher than 75 kW/t (102 hp per ton), an excess of four decibels is allowed. If there is more than 110 kW (almost 150 hp) per ton, the tests are carried out in a gentle manner, only at a constant speed. A lot of civilian cars fit into this framework. Even the not-so-powerful 145-horsepower Lada Vesta Sport has 109 hp per ton. Why, then, is there a fuss made about internal noise certification, forcing manufacturers to incur unnecessary costs that will eventually be included in the car’s price?
It is curious that not a word is usually said about noise and vibration in textbooks on the theory of cars of Soviet times. The fight against them was often conducted on the residual principle: when both the body and the engine were ready, designers began to look: how to make the interior quieter? For example, they added the same insulation by skipping the first two steps: the fight against the source of disturbances and their propagation. Today, a competitive car can be built only if the manufacturer thinks about NVH at the layout stage, not to mention the design.
Modern technologies pose new challenges to acoustic engineers. Active lightening of bodies, the use of light materials such as aluminum alloys or composites contribute to an increase in structural noise. Tires are getting wider ― and therefore louder. In the pursuit of environmental friendliness, the process of fuel combustion in the cylinder often becomes less smooth ― that is, it generates more vibrations.

The abandonment of the internal combustion engine in favor of the electric motor doesn’t make the task easier. Instead of the usual 2500-3000 Hz, the frequency spectrum emitted by the engine is in the uncomfortable range of about 5000 Hz, where a new type of noise is mixed with it ― electromagnetic. There are new sounds that were previously ignored, because they were drowned out by the internal combustion engine. For example, those created by climate control dampers. If we look even further into the driverless future imposed on us, the role of NVH will only grow, because there will be almost nothing to discuss in addition to the acoustic comfort in the car. And noise is a substance that seems to be understandable to each of us…
You can read the original here: https://www.drive.ru/technic/5ebe5f04ec05c49c7e0000eb.html
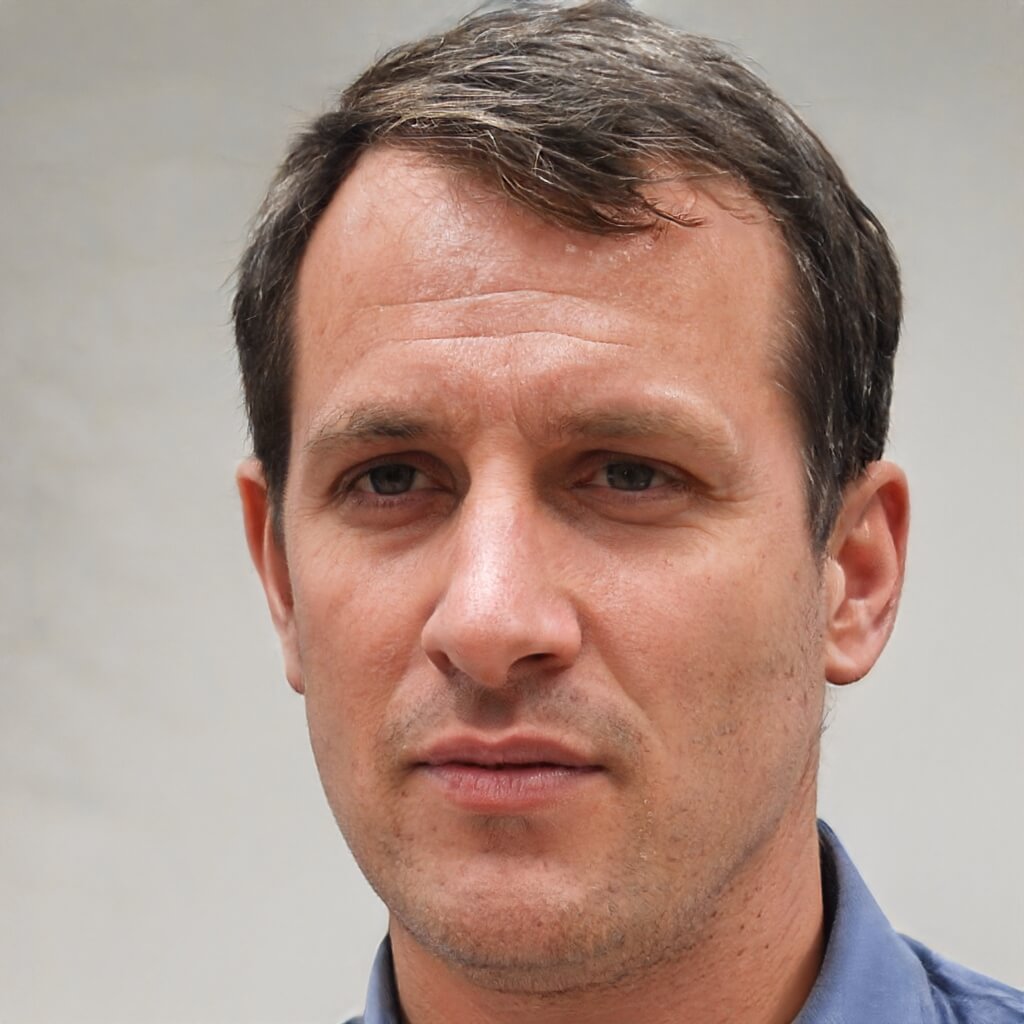
Published August 19, 2021 • 11m to read