Many people know about the benefits of changing the gas distribution phases of the internal combustion engine at inlet and (or) outlet. Now such engines are common. Sometimes they are supplemented with a device that changes the height of the valve lift. And yet, there is no complete freedom of regulation. After all, smart actuators don’t act on the valves themselves, but shift camshafts, the rotation of which is connected with the rotation of the crankshaft, by several degrees. Or such systems transfer the operation of the valve from one cam to another with a different profile. Another technology allows you to free the phase control from any limits: Intelligent Valve Actuation (IVA) from the British company Camcon Auto.
In such an intelligent actuator, the camshaft, which is individual for each valve, doesn’t rotate constantly, but turns only when the valve needs to be opened or closed. And it turns first in one direction, and then in the other. The cam is connected to the valve by a desmodromic valve control. That is, the reverse stroke is carried out not due to the spring, but, again, is tightly controlled by the camshaft. The valve can be opened much faster than in a conventional internal combustion engine, then left almost stationary, then closed. You can make it open twice in one stroke of piston. Or you can change the order of ignition in the cylinders with one software. You can also set a personal lifting and lowering profile for each cylinder and change it at any time.
A conventional internal combustion engine with the IVA technology can implement any thermodynamic cycle at the request of programmers — Otto, Miller/Atkinson, Homogeneous Charge Compression Ignition, its Mazda version – Spark Controlled Compression Ignition. Such an engine can be easily switched from a four-stroke cycle to a two-stroke cycle or even to a super-efficient 12-stroke cycle by changing the program. The latter is a variation on the long-standing idea of turning off part of the cylinders under low load. But in conventional internal combustion engines, the electronics deactivate, for example, half of the cylinders for a certain long time. And in the case of IVA, all cylinders work evenly. But each of them gets fuel and turns on the ignition not once in four cycles, but on every third working stroke (once in 12 cycles). Thus, all cylinders remain at their normal operating temperature.
Of course, Camcon is not the first company to think about a system of complete and absolutely free control over the gas distribution phases. Such projects existed at GM and Ford, Ricardo and Lotus Engineering. From the latest examples, we need to recall the Qamfree system without a single camshaft. That development began in Koenigsegg, and continued in the company FreeValve together with Qoros. In Camcon Auto, as we can see, they went the opposite way — they put a personal camshaft on each valve.
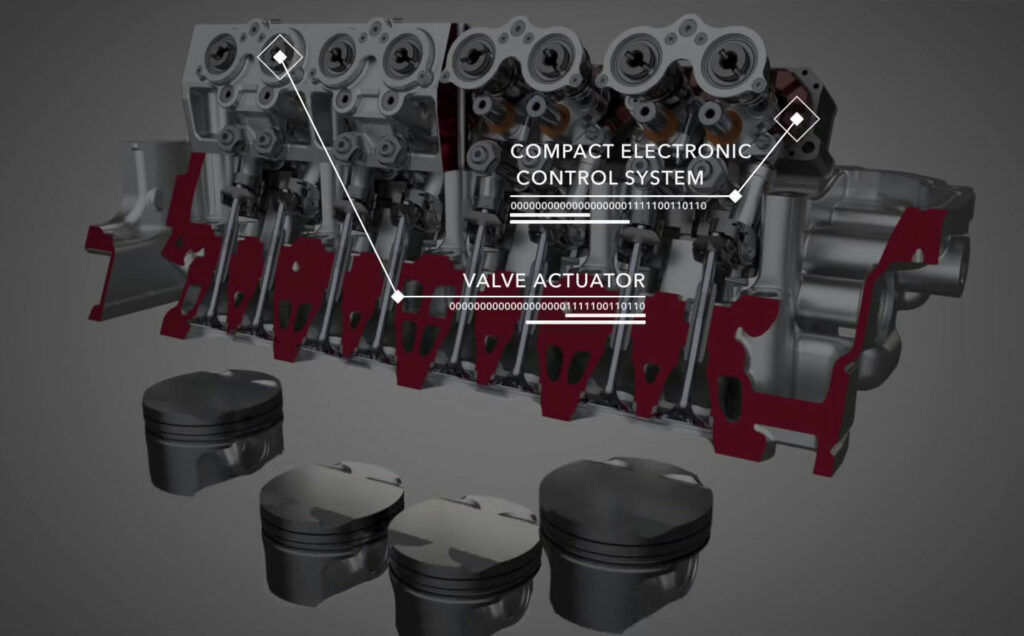
According to the developers, the IVA system can potentially reduce carbon dioxide emissions by 15-20%. They managed to demonstrate a fuel economy of 7.5% on the prototype engines (turbocharged four-cylinder 2.0). In the series, IVA would be cheaper than a hybrid power unit, according to the British. And the consumption of cars with a gasoline unit would be approximately comparable to a diesel engine. Camcon is ready to supply manufacturers with sets of its actuators and kits for adapting them to engines, or to cooperate with component suppliers. The British predict that IVA will appear on production cars within five years.
This is a translation. You can read the original here: https://www.drive.ru/technic/5be19fd7ec05c4bb5c00003d.html
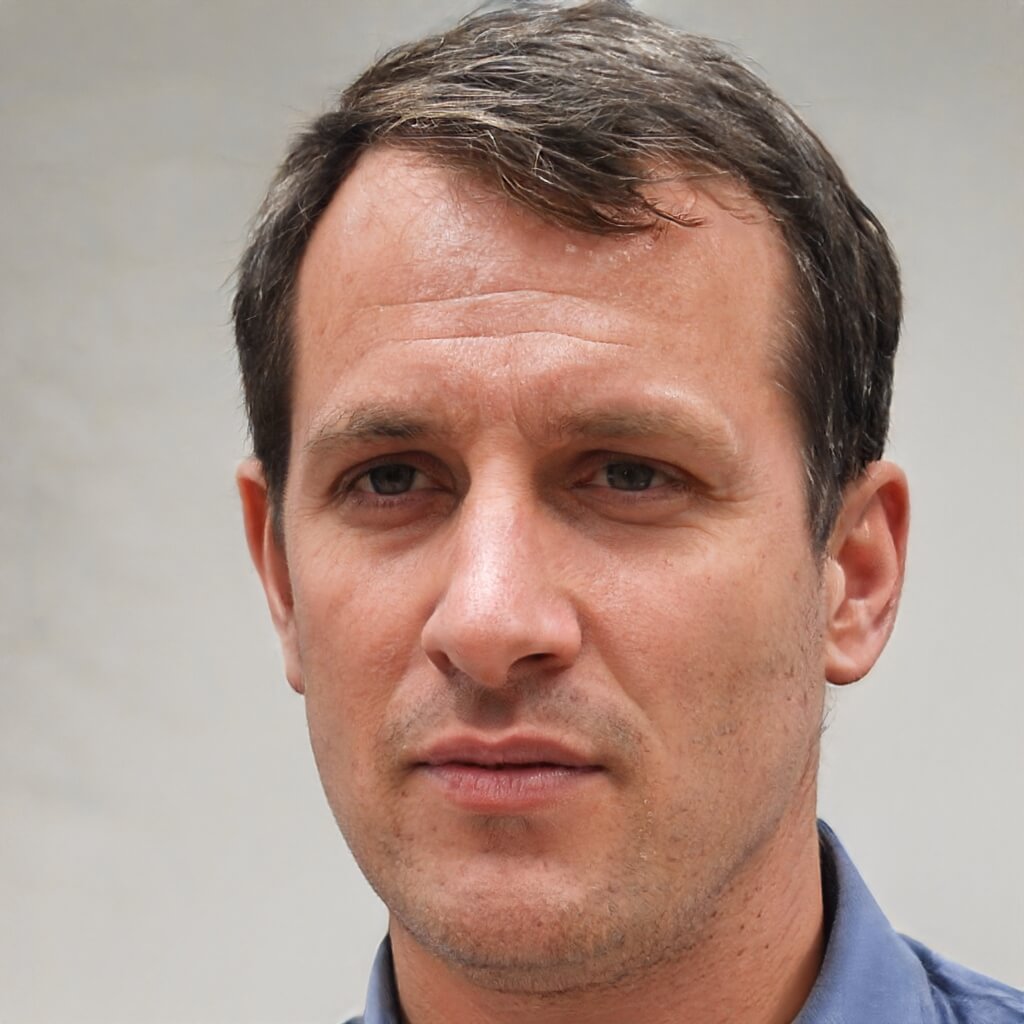
Published September 16, 2021 • 3m to read