È indubbio che ognuno di noi abbia notato almeno una volta nella vita la targhetta “turbo” su un’auto dall’aspetto ordinario. Quasi di proposito, i costruttori realizzano queste targhette di dimensioni ridotte e in punti poco appariscenti, in modo che un passante non esperto non le noti e passi oltre. Una persona consapevole, invece, si fermerà sicuramente e si interesserà all’auto. Qui di seguito vengono spiegate le ragioni di questo comportamento.
I progettisti automobilistici (fin dalla nascita di questa professione) si preoccupano costantemente del problema dell’aumento di potenza del motore. Le leggi della fisica stabiliscono che la potenza del motore dipende direttamente dalla quantità di carburante bruciata in un ciclo di lavoro. Più carburante si brucia, maggiore è la potenza. E se vogliamo aumentare il “numero di cavalli” sotto il cofano, come fare? È qui che si presentano i problemi.
Il fatto è che l’ossigeno è necessario per la combustione del carburante. Quindi non si tratta di un carburante, ma di una miscela carburante-aria che brucia nei cilindri. È necessario miscelare il carburante con l’aria non a occhio, ma in un certo rapporto. Ad esempio, una miscela per motori a benzina è composta da una parte di carburante e 14-15 parti di aria – a seconda della modalità di funzionamento, della composizione del carburante e di altri fattori.
Come si vede, è necessaria molta aria. Se aumentiamo l’apporto di carburante (non è un problema), dovremo anche aumentare in modo significativo l’apporto di aria. I motori convenzionali la aspirano da soli grazie alla differenza di pressione nel cilindro e nell’atmosfera. La dipendenza è diretta: più grande è il volume del cilindro, più ossigeno vi entrerà ad ogni ciclo. È quello che hanno fatto gli americani, producendo motori enormi con consumi da capogiro. Ma esiste un modo per pompare più aria nello stesso volume?
Esiste, ed è stato inventato dal signor Gottlieb Wilhelm Daimler. Questo cognome vi è familiare? Certo, è utilizzato nel nome DaimlerChrysler. Questo tedesco era molto bravo con i motori e, nel 1885, inventò il modo di pompare più aria al loro interno. Gli venne l’idea di pompare aria nei cilindri utilizzando un compressore, ovvero una ventola (compressore) che riceveva la rotazione direttamente dall’albero del motore e pompava aria compressa nei cilindri.
L’ingegnere e inventore svizzero Alfred J. Büchi si spinse oltre. Era responsabile dello sviluppo dei motori diesel presso l’azienda Sulzers Brothers e non gli piaceva affatto che i motori fossero grandi e pesanti e sviluppassero poca potenza. Inoltre, non voleva sottrarre energia al motore per far ruotare il compressore. Pertanto, nel 1905, Büchi brevettò il primo dispositivo di ricarica dell’aria al mondo, che utilizzava l’energia dei gas di scarico come fonte di energia. In poche parole, inventò la sovralimentazione.
L’idea dell’intelligente svizzero è tanto semplice quanto geniale. I gas di scarico fanno ruotare una ruota a pale come i venti fanno girare le vele del mulino. L’unica differenza è che la ruota è molto piccola e le pale sono molte. La ruota a pale si chiama rotore della turbina ed è montata sullo stesso albero della ruota del compressore. Convenzionalmente, il turbocompressore può essere diviso in due parti: un rotore e un compressore. Il rotore riceve la rotazione dai gas di scarico e il compressore ad esso collegato pompa aria supplementare nei cilindri, funzionando come una “ventola”. Tutta questa complessa struttura è chiamata turbocompressore (dalle parole latine “turbo” – vortice e “compressio” – compressione).
In un motore con turbocompressore, l’aria che entra nei cilindri deve spesso essere ulteriormente raffreddata e la sua pressione può essere aumentata pompando più ossigeno nel cilindro. Dopo tutto, è più facile comprimere l’aria fredda (già presente nel cilindro del motore a combustione interna) che quella calda.
L’aria che passa attraverso la turbina è riscaldata dalla compressione e dalle parti del turbocompressore riscaldate dai gas di scarico. L’aria fornita al motore viene raffreddata con l’uso di un intercooler. Si tratta di un radiatore installato sul percorso dell’aria dal compressore ai cilindri del motore. Passando attraverso di esso, cede il suo calore all’atmosfera. L’aria fredda è più densa e quindi può essere pompata nei cilindri in quantità ancora maggiore.
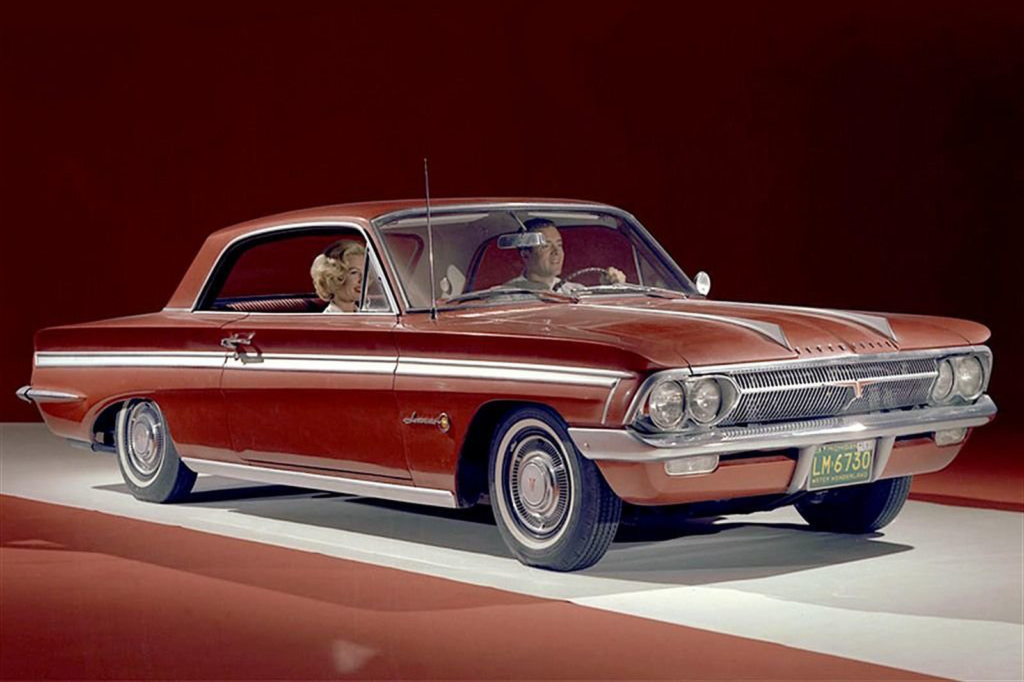
Più gas di scarico entrano nella turbina, più questa ruota velocemente e più aria supplementare entra nei cilindri, più alta è la potenza. L’efficienza di questa soluzione rispetto, ad esempio, a un compressore a trazione è che pochissima energia del motore, solo l’1,5%, viene spesa per “l’auto-manutenzione” della carica. Il fatto è che il rotore della turbina riceve energia dai gas di scarico non attraverso il loro rallentamento, ma attraverso il loro raffreddamento: dopo la turbina, i gas di scarico sono ancora veloci, ma più freddi. Inoltre, l’energia gratuita spesa per la compressione dell’aria aumenta l’efficienza del motore. E la capacità di ottenere più potenza da un volume di lavoro più piccolo significa meno perdite per attrito, meno peso del motore (e dell’auto nel suo complesso). Tutto ciò rende le auto con turbocompressore più efficienti dal punto di vista dei consumi rispetto alle loro controparti atmosferiche di pari potenza. Sembrerebbe una felicità. Ma no, non è così semplice. I problemi sono appena iniziati.
In primo luogo, la velocità di rotazione della turbina può raggiungere i 200 mila giri al minuto e, in secondo luogo, la temperatura dell’incandescenza raggiunge, provate a immaginare, i 1000°C! Cosa significa tutto questo? È molto costoso e difficile realizzare un turbocompressore in grado di sopportare carichi così elevati per lungo tempo.
Per questi motivi, il turbocompressore si è diffuso solo durante la Seconda Guerra Mondiale, e solo nell’aviazione. Negli anni ’50, l’azienda americana Caterpillar riuscì ad adattarla ai suoi trattori e i maestri della Cummins progettarono i primi turbodiesel per i loro camion. I motori turbo apparvero sulle autovetture di serie anche più tardi. Accadde nel 1962, quando la Oldsmobile Jetfire e la Chevrolet Corvair Monza uscirono quasi contemporaneamente.
Ma la complessità e il costo elevato del progetto non sono gli unici inconvenienti. Il fatto è che l’efficienza della turbina dipende fortemente dalla velocità del motore. A bassa velocità, il volume dei gas di scarico è scarso, il rotore ruota male e il compressore non soffia quasi più aria nei cilindri. Pertanto, accade che il motore non vada affatto a meno di tremila giri/minuto e solo dopo quattro o cinquemila “scatti”. Questo inconveniente si chiama ritardo del turbocompressore. Inoltre, quanto più grande è la turbina, tanto più a lungo raccoglierà la velocità. Pertanto, i motori con un rapporto peso/potenza molto elevato e con turbine ad alta pressione, di norma, soffrono particolarmente del ritardo del turbocompressore. Le turbine che creano bassa pressione, invece, non hanno quasi nessun turbo-lag, ma non aumentano troppo la potenza.
Uno schema di sovralimentazione sequenziale aiuta a eliminare quasi del tutto il turbo-lag. A bassi regimi, un piccolo turbocompressore a bassa inerzia funziona, aumentando la spinta ai “bassi”, e il secondo, più grande, si attiva ad alti regimi con un aumento della pressione di scarico. Nel secolo scorso, un turbocompressore sequenziale è stato utilizzato sulla Porsche 959 e oggi, ad esempio, i turbodiesel di BMW e Land Rover sono disposti secondo questo schema. Nei motori a benzina Volkswagen, il ruolo di piccola “centrale elettrica” è svolto da un sovralimentatore di trazione.
Nei motori rettilinei, viene spesso utilizzato un singolo turbocompressore twin-scroll (una coppia di volute) con un doppio apparato di lavoro. Ciascuna delle volute viene riempita con i gas di scarico di diversi gruppi di cilindri. Ma allo stesso tempo, entrambe alimentano i gas a una turbina, facendola ruotare sia a bassa che ad alta velocità.
Ma è ancora più comune trovare una coppia di turbocompressori identici che servono gruppi di cilindri separati in parallelo. Uno schema tipico dei motori turbo a V, in cui ogni unità ha il proprio compressore. Anche se il motore V8 di M GmbH, che ha debuttato sulle BMW X5 M e X6 M, è dotato di un collettore di scarico cross-bank, che consente al compressore twin-scroll di ricevere i gas di scarico dai cilindri di blocchi diversi che operano in fase opposta.
È inoltre possibile far funzionare il turbocompressore in modo più efficiente nell’intera gamma di velocità modificando la geometria dell’organo di lavoro. A seconda del numero di giri all’interno della voluta, ruotano speciali pale e varia la forma dell’ugello. Il risultato è una “superturbina” che funziona bene nell’intera gamma di velocità. Queste idee erano nell’aria da decenni, ma sono state realizzate relativamente di recente. Inoltre, le prime turbine a geometria variabile sono apparse sui motori diesel, dove fortunatamente la temperatura dei gas è molto più bassa. La Porsche 911 Turbo è stata la prima auto a benzina a provare una turbina di questo tipo.
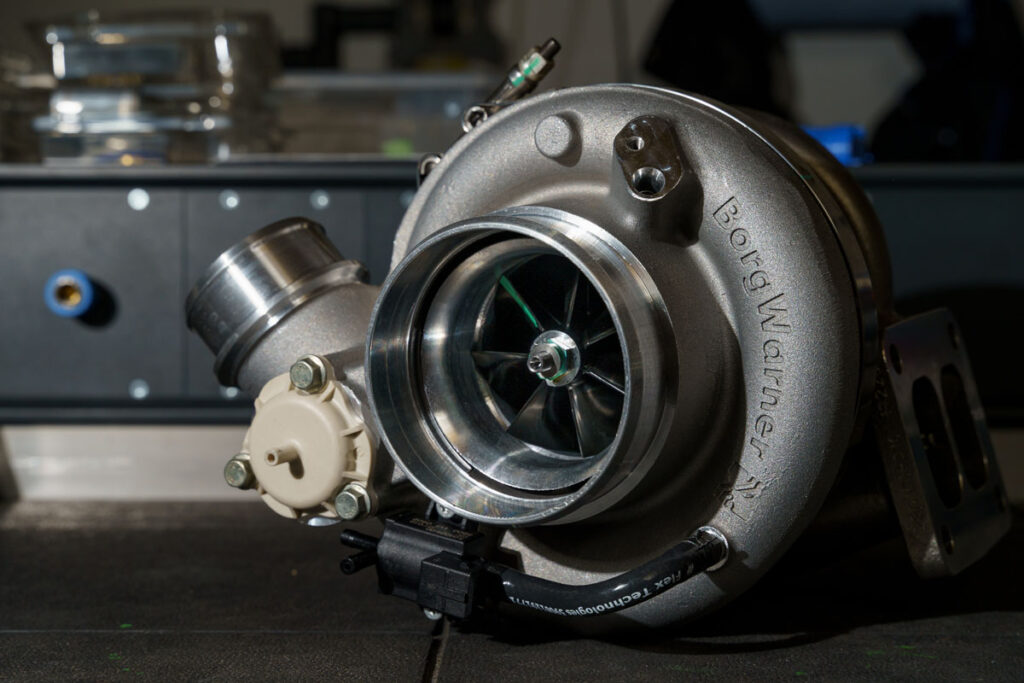
La progettazione dei motori turbo ha preso forma molto tempo fa e di recente la loro popolarità è aumentata notevolmente. Inoltre, i turbocompressori si sono rivelati promettenti non solo in termini di forzatura del motore, ma anche di aumento dell’efficienza e della purezza dello scarico. Questo è il caso soprattutto dei motori diesel. Oggi quasi tutti i diesel hanno il prefisso turbo. Allo stesso tempo, l’installazione di una turbina sui motori a benzina consente di trasformare un’auto dall’aspetto ordinario in una vera e propria “accendino”. Quella con una piccola e appena percettibile targhetta “turbo”.
Questa è una traduzione. Potete leggere l’originale qui: https://www.drive.ru/technic/4efb330200f11713001e3303.html
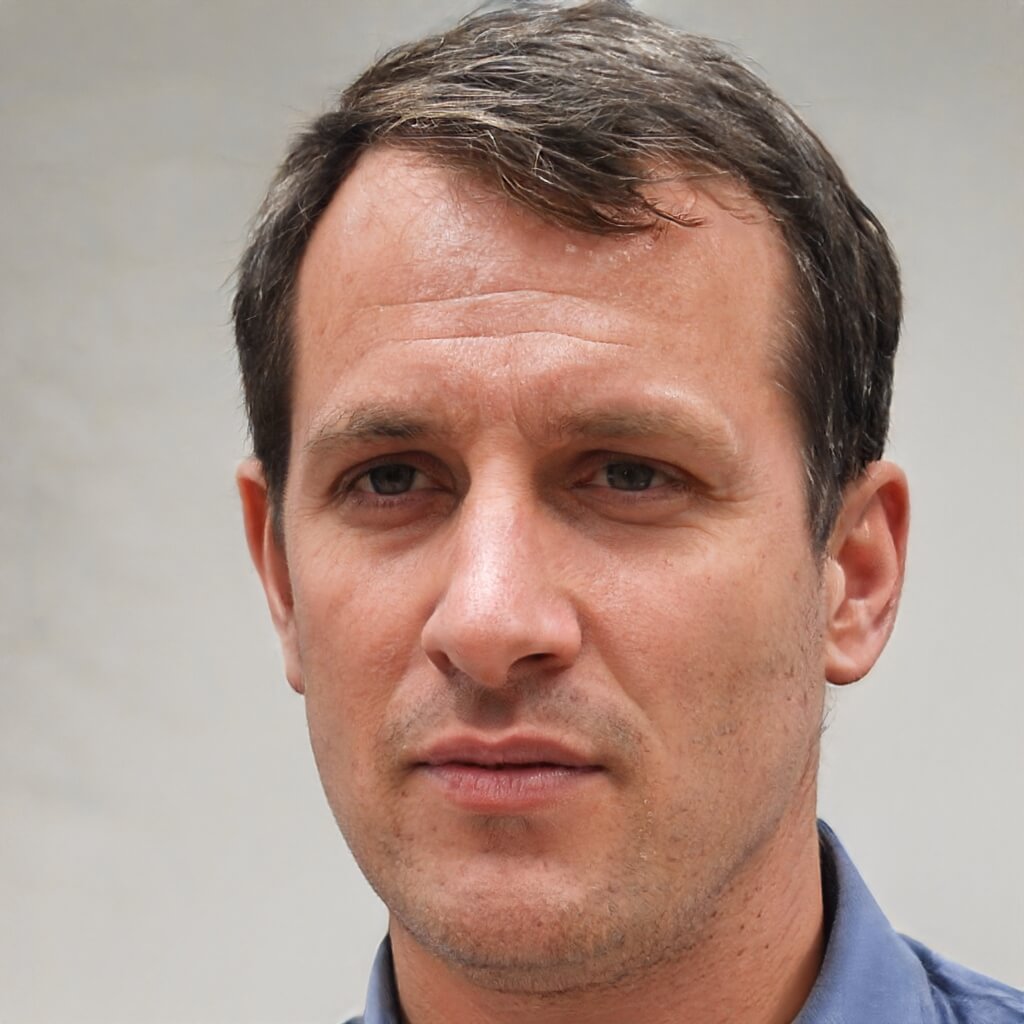
Pubblicato Gennaio 27, 2022 • 8m da leggere