Strange engines stuck on the margins of progress
The Wankel engine, the Stirling engine, and various types of turbo-power units never entered the automotive mainstream. A number of well-known companies (from Mazda to GM, from Mercedes to Volvo) worked on them for decades, small firms and individual inventors also persisted. Alas, it turned out that there were much more pitfalls in a particular design than it seemed at first. But this doesn’t mean that the development of alternative power units is impossible. Enthusiasts run through different ideas, and we would like to share with you a number of exotic schemes.
Some creators of promising engines decided that the combination of cylinder, piston, connecting rod and crankshaft has proven itself for more than a century and it is not necessary to reinvent it in order to improve the parameters of the internal combustion engine — it is enough just to correct some aspects. Therefore, the first in our list is the engine of the American company Scuderi Group, which has classic intake, compression, power and exhaust strokes, but they occur not in the same cylinder, but in different ones. The so-called cold cylinder is responsible for the intake and compression, and the second, hot one, – for the power stroke and exhaust.
While there is a gas expansion in the working cylinder, an intake stroke takes place in the cold, compressor one. An exhaust in the working one, a compression in the cold one. At the end of the compression stroke, the pistons approach their upper dead centers, a mixture moves through the bypass channel from the cold cylinder to the hot one and is ignited. Such a split cycle (in principle, the Otto cycle, albeit modified) was invented by the Americans in 2006, and in 2009, they built the pilot Scuderi Split Cycle Engine. The compressor and working cylinders can have different diameters and strokes of the pistons, which makes it possible to flexibly adjust the parameters – it is an analog of the Miller cycle with additional gas expansion.
If you add a branch with valves and a high-pressure bottle to the channel between the cylinders, you can make such a motor gather energy during braking and use it during acceleration. However, for a number of years, Scuderi Group’s activities have been limited only to prototypes and participation in exhibitions. It seems that the real efficiency still can’t beat the high complexity of the design here.
The developers of the Croatian company Paut Motor also turned to the split working cycle. Their “spaced” design attracted attention with fewer parts, low friction, and reduced noise. And the need for an external tank for the lubrication system, caused by the fact that there is no oil in the crankcase, didn’t frighten. The inventors built several prototypes. With a capacity of seven liters, their dimensions (500×440×440 mm) and weight (135 kg) are almost half that of traditional internal combustion engines. But the output was never determined. The last prototype was assembled in 2011, and then the project stalled.
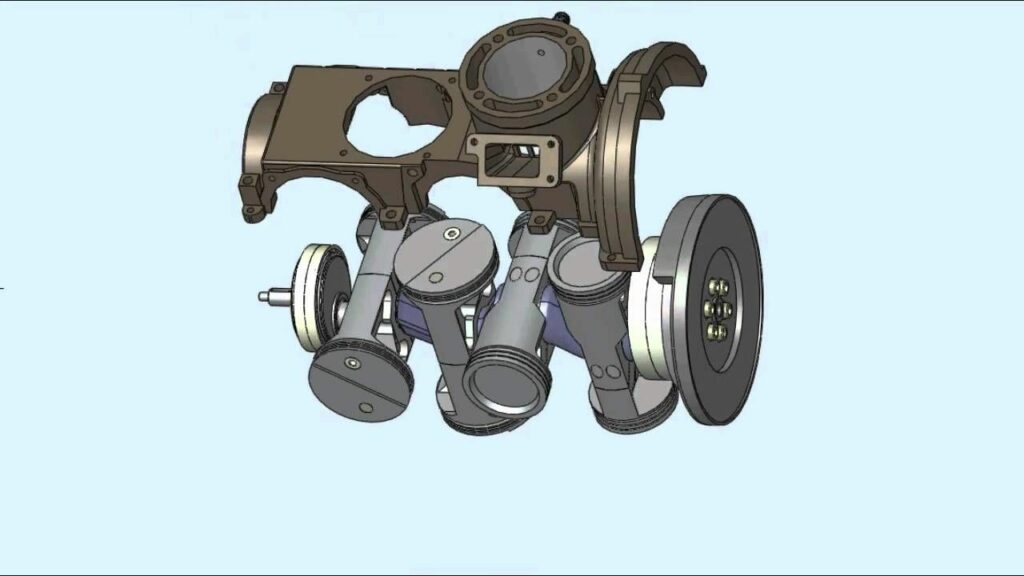
The Bonner two-stroke engine (named after the sponsor, Bonner Motor), invented in 2006 in the United States by Walter Schmid, is even more complicated. As in the Paut Motor project, the cylinders are arranged in the shape of the letter X here, and the crankshaft also performs planet motion due to the gear system.
Valves in cylinder bottoms and rotating spool valves in the motor body are responsible for the gas distribution in Bonner. At the same time, external pistons can shift slightly under the oil pressure, providing a variable compression ratio. What a complicated scheme! And all this is for the sake of high power per unit of weight. In theory, Bonner looks interesting, but in practice, there has been no news about it for a long time — apparently, it hasn’t met the expectations.
Other inventors didn’t change the working cycles of the internal combustion engine, but focused on the location of its parts. These are, for example, axial motors which are more than a hundred years old. They all differ in details, but are united by a common principle — the cylinders are arranged like cartridges in a revolver cylinder, with a coaxial output shaft. Different systems, such as pins inclined to the longitudinal axis of the engine, taper washers, and the like, are responsible for converting the reciprocating motions of the pistons into the rotation of the shaft.
A New Zealand project of the company Duke Engines, a five-cylinder four-stroke engine with a capacity of three liters, is a variety of axial units. Compared to the classic internal combustion engine of the same capacity, this one was, according to the authors’ calculations, 19% lighter and 36% more compact. It was promised to be used in a variety of fields, but dreams of conquering the whole world remained dreams.
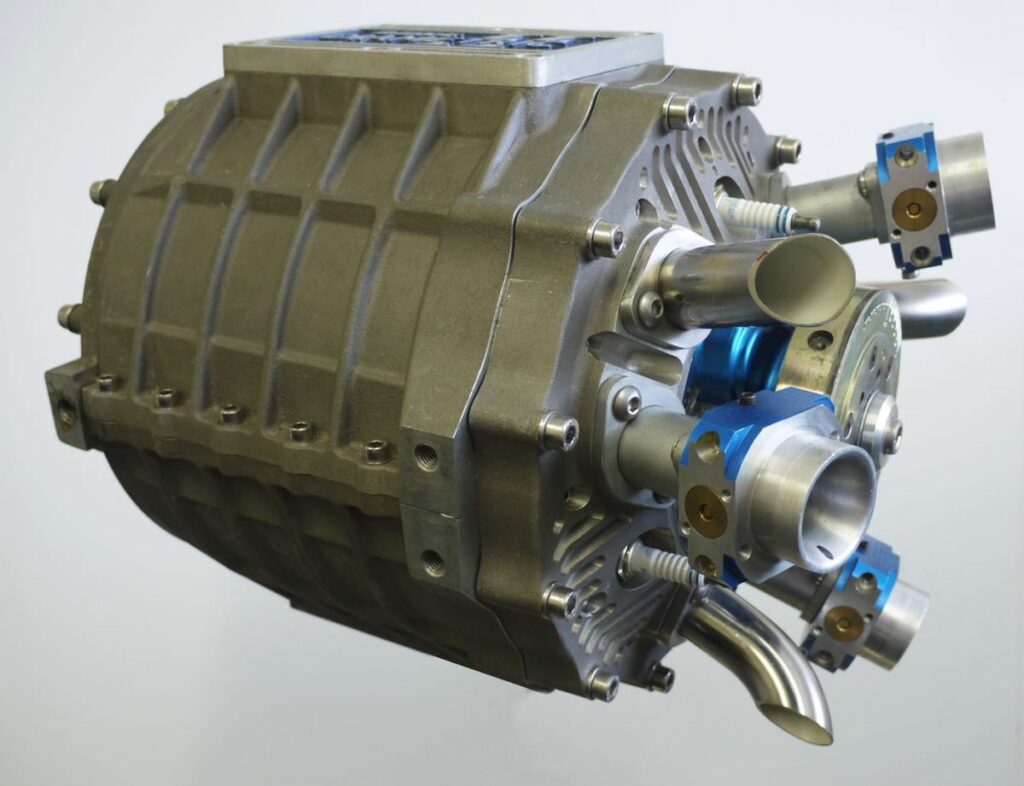
The RadMax engine of the Canadian company Reg Technologies is an even more complex axial example. Here, instead of cylinders, a dozen compartments are organized in a common drum with the help of thin blades. In slots of the rotor, plates are installed that move along them as it rotates. The resulting variable volumes limit the curved surfaces at the ends: they set the trajectory of the blades and control the gas exchange.
The RadMax scheme makes it possible to create engines for different types of fuel, although initially the inventors chose diesel. In 2003, a prototype was built with a diameter and a length of only 152 mm. It developed 42 horsepower – many times more than a similar-sized internal combustion engine. Later, the company reported on the creation of larger prototypes with 127 and 380 horsepower. But, judging by the releases, all its activities still don’t go beyond experiments.
Toroidal Round Engine (or VGT Engine) of the already disappeared Canadian company VGT Technologies is another example of the superiority of theory over practice. The first prototypes of the engine with a toroid of variable geometry (hence the letters VGT — Variable Geometry Toroidal Engine) were tested by engineers back in 2005.
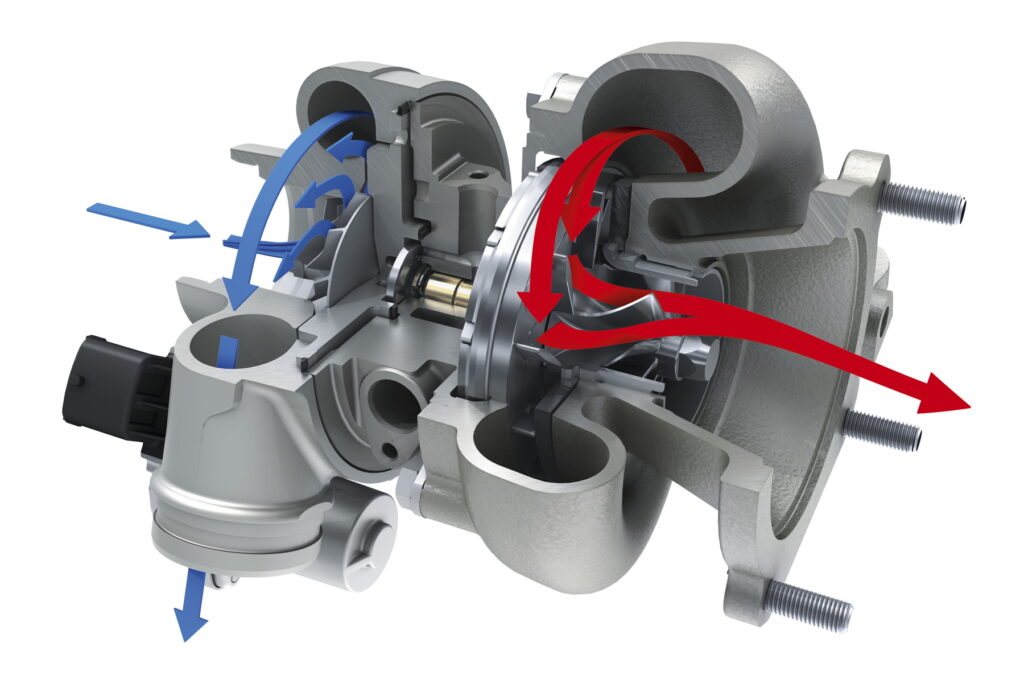
The toroid here plays the role of a cylinder, inside which a rotor rotates with a pair of pistons attached to it. The variable volumes necessary to ensure power strokes are formed between the pistons by means of a thin distribution disk with a cutout for the pistons which rotates across the toroid with a belt drive or other. This disk restricts a fuel-air mixture during compression and power stroke.
In 2009, American entrepreneurs, Gary Kelley and Rick Ivas, developed their toroidal engine, essentially recreating the Canadian one. According to their estimates, a half-meter diameter toroid would provide 230 hp and about 1000 N⋅m at only 1050 rpm. But… there is a stub on the website of their company Garric Engines now: “Thank you for your interest. The page may be updated in the future.” Perhaps a slightly better fate awaits the so-called nutating engine invented by the American Leonard Meyer in 2006 – at least it was built in several copies.
The name of the engine originates from the Latin nutatio. Meyer formed four working chambers of variable volume between the motor body and the nutating to the sides disk which plays the role of a piston. The disk is cut in half along its diameter and strung on a Z-shaped shaft which produces power. Channels and valves in the body are responsible for gas exchange.
Prototypes of Meyer’s engine were built by Baker Engineering and its sister company Kinetic BEI. The unit develops seven hp with a single disk with a diameter of 102 mm, and already 120 with a pair of 203 mm disks! The length of the two-disk engine is 500 mm, the diameter is 300 mm, and the capacity is 3.8 liters. 2.5-3 horsepower per kilogram against one or two for mass-produced atmospheric internal combustion engines (among non-mass engines, some Ferrari engines produce more than three hp per kilogram, but at high 9000 rpm). However, the liter capacity is not impressive. Now Baker and Kinetic seem to whip the projects into shape, although there is not much activity on their websites.
The idea of rotary units of various types so often attracts innovators, as if just a departure from the familiar scheme gives a significant increase in performance. So, Nikolay Shkolnik, a native of the USSR who moved to the United States a long time ago, with his son Alexander developed an engine that resembles the Wankel engine turned inside out. The peanut-shaped rotor rotates in a triangular chamber the same way, but unlike the Wankel unit, the seals are fixed not to the piston, but to the chamber walls.
To develop the design, the Shkolniks founded the company LiquidPiston, which attracted the DARPA — now it co-finances experiments with a view to the operation of “peanut” units in light aircraft, including drones, and in portable generators. A prototype motor with a capacity of 23 cm3 has a good efficiency of 20% for such dimensions. Now the authors are aiming for a diesel prototype weighing about 13 kg and producing 40 hp for installation on a hybrid car. Its efficiency will allegedly grow to 45%.
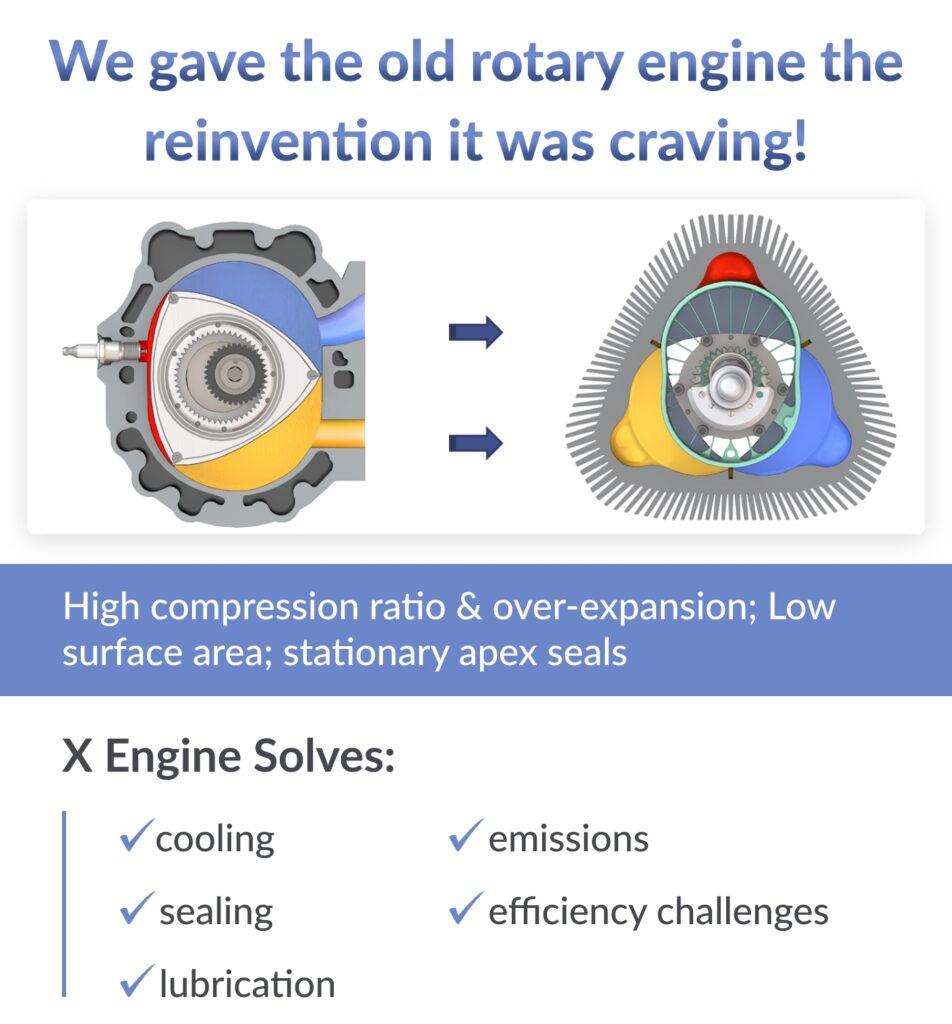
The last engine we will review demonstrates that the idea of a flat unit (because the rotor can be made very narrow) is tempting. At the same time, the rotors themselves are not so necessary for its implementation — it is enough to square the traditional piston and, accordingly, make the cylinder rectangular in the top view.
This strange development of the company Pivotal Engineering has existed for several years, during which a number of prototypes were created that geared motorcycles and airplanes. The authors address the so-called swinging piston primarily to aviation. In addition to the high output characteristics in relation to weight and dimensions, such a two-stroke unit is perfectly capable of forcing due to the passage of a liquid cooling channel through the fixed axis of the piston. Such a trick is difficult with a different scheme.
There are many exotic developments outside of our review, like the 12-rotor Wankel engine, the Knight engine or units with opposed pistons, internal combustion engines with a variable compression ratio or with five strokes (there are also such ones!), and also rotary-bladed units in which the components of the rotor make movements like converging and diverging scissors blades.
Even a cursory excursion beyond the limits of classical internal combustion engines has shown how many ideas aren’t implemented in mass production. Rotors are often ruined by the problem of seal wear. Rotary-bladed options also suffer from high alternating loads that destroy the mechanism of connection between the blades and the shaft. This is just one of the reasons why we don’t see such “miracles” on production cars.
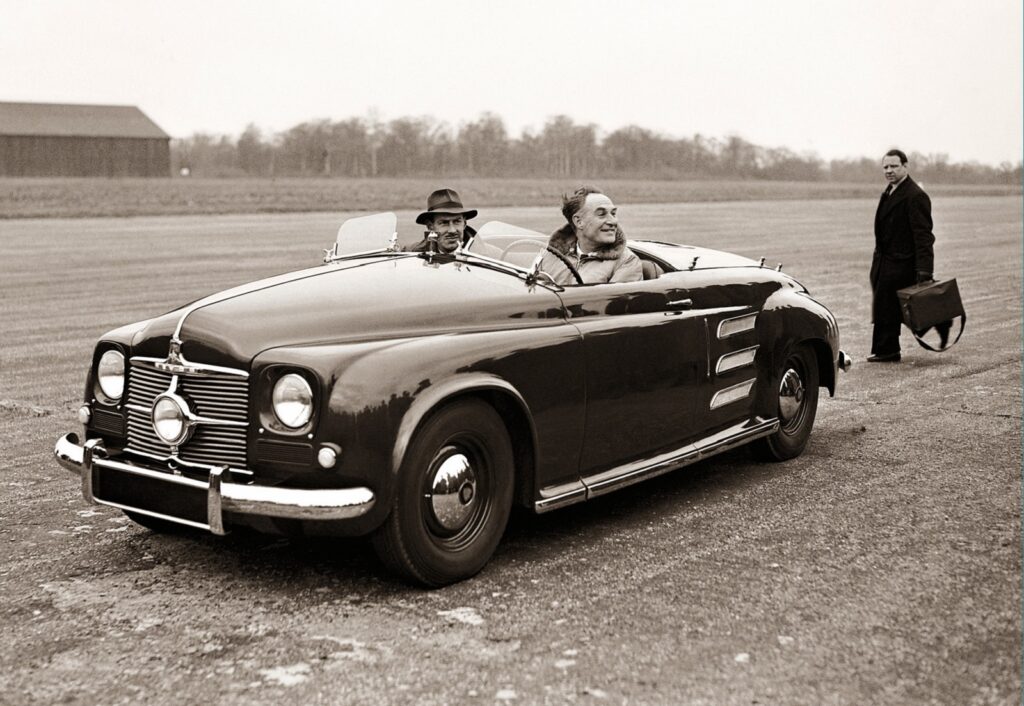
The second reason is that the production of traditional internal combustion engines doesn’t stand still. In the latest gasoline samples with the Miller cycle, the thermal efficiency reaches 40% even without turbocharging. That’s a lot. Most gasoline units have 20-30%. Diesel engines – 30-40% (on large ships — up to 50). And most importantly – a global alternative to the internal combustion engine has already been found. These are electric motors and fuel cell power units. Therefore, if the inventors of curiosities don’t solve all the technical problems in the very near future, they simply won’t be able to taxi off the margins of progress in front of electric cars.
This is a translation. You can read the original here: https://www.drive.ru/technic/57769ed4ec05c4745f00009b.html